Gemba walks, a cornerstone of lean manufacturing principles, offer invaluable insights for prefabrication shop leaders. By going to the actual place where work happens, managers can gain a deep understanding of processes, identify inefficiencies, and drive meaningful improvements.
Walk the Floor to Prefab More
how Gemba walks help unlock efficiency in your prefab processes
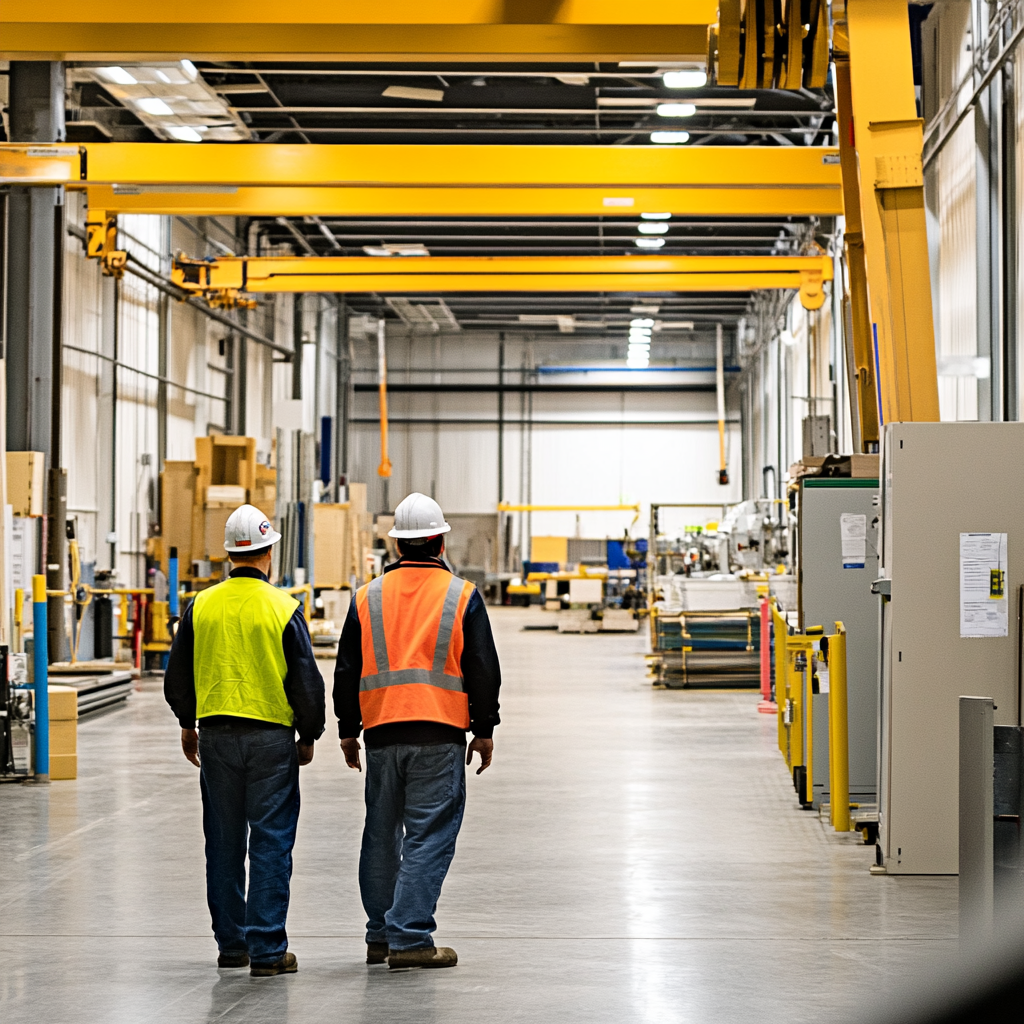
The Importance of Gemba Walks
Gemba walks serve multiple crucial purposes in prefabrication operations. They allow leaders to observe processes firsthand, identify inefficiencies and bottlenecks, engage directly with employees, and foster a culture of continuous improvement. By regularly conducting Gemba walks, leaders can bridge the gap between management perceptions and shop floor realities, leading to more informed decision-making and a more engaged workforce.It's crucial to emphasize that Gemba walks are about analyzing processes, not people. The focus should always be on understanding how the work is done and identifying opportunities for improvement, rather than critiquing individual performance.
Preparing for Your Gemba Walk
Effective Gemba walks require thoughtful preparation. Before embarking on your walk, set clear objectives by defining specific goals, such as improving a particular process or addressing a known issue. Schedule strategically by choosing a time when production is in full swing to observe typical operations. Finally, inform the team by communicating the purpose of the walk to employees, emphasizing its collaborative nature and focus on process improvement. By taking these preparatory steps, you create an environment conducive to open communication and meaningful observations during the walk.
Conducting an Effective Gemba Walk
Observe and Engage
The heart of a Gemba walk lies in careful observation and meaningful engagement with employees. As you walk through the prefabrication shop, watch the workflow without interrupting, ask open-ended questions to understand processes, and listen actively to employee concerns and suggestions. This approach allows you to gather authentic insights while demonstrating respect for the expertise of your frontline workers. Remember, the goal is to understand the process, not to evaluate individual performance.
Key Areas to Focus On
During your Gemba walk, pay particular attention to critical aspects of prefabrication operations, including material flow and inventory management, workstation layout and ergonomics, quality control processes, and safety practices. By focusing on these areas, you can identify opportunities for improvement that have a significant impact on overall efficiency and quality.
Post-Walk Actions
To maximize the benefits of your Gemba walk, follow these steps after completing your observations. First, analyze your observations by reviewing your notes and identifying key improvement opportunities in processes and workflows. Then, develop action plans by creating specific, measurable steps to address identified issues. Next, communicate findings by sharing insights with both the team and leadership to ensure alignment. Finally, follow up by scheduling regular walks to monitor progress and identify new opportunities. This structured approach ensures that insights gained during the walk translate into tangible improvements in your prefabrication operations.
Streamlining Material Flow
Observation: During a Gemba walk in the panel assembly area, you notice workers frequently leaving their stations to fetch materials from a centralized storage area. This is causing significant downtime and disrupting the production flow.
Questions Asked:
- How often do you need to leave your station to get materials?
- What materials do you find yourself fetching most frequently?
- How much time do you estimate you spend retrieving materials each day?
- Have you considered any ways to reduce these trips?
After discussing the issue with the workers, several potential solutions emerged. These included implementing a kanban system for just-in-time material delivery, redesigning the workstation layout to include nearby material storage, and assigning a dedicated material handler to supply workstations. After careful consideration, the team decided to implement a kanban system for just-in-time material delivery.
The implementation involved installing digital kanban boards at each workstation, setting up a centralized material handling team, creating standardized material kits for each assembly type, and training workers and material handlers on the new system. As a result, the shop expected to see reduced downtime, increased productivity, improved worker satisfaction due to less time spent on non-value-added tasks, and a more consistent production flow.
Enhancing Quality Control
Observation: While observing the welding station, you identify inconsistencies in weld quality checks. Some workers are performing thorough inspections, while others are rushing through the process, potentially missing defects.
Questions Asked:
- What is the current quality check procedure?
- How were you trained on quality inspection?
- Do you feel you have enough time to perform thorough checks?
- What tools or resources would help you perform more consistent inspections?
The team discussed various solutions to address this issue, including developing standardized inspection checklists, implementing automated weld inspection technology, providing comprehensive training on quality control procedures, and increasing inspection time allowances in the production schedule. After weighing the options, they decided to develop standardized inspection checklists and provide comprehensive training.
This solution involved creating detailed, step-by-step inspection checklists for each weld type, designing and delivering a training program on quality control procedures, implementing a buddy system for newer welders to learn from experienced inspectors, and conducting regular audits to ensure compliance with new procedures. The expected results included improved product quality with reduced defect rate, increased consistency in quality checks across all shifts, enhanced skills and confidence of the welding team, and reduced rework and associated costs.
Improving Safety
Observation: In the cutting area, you notice workers struggling with heavy materials, often adopting awkward postures that could lead to injuries.
Questions Asked:
- How often do you handle heavy materials in your work?
- Have you experienced any discomfort or strain while performing these tasks?
- What current methods or tools do you use to assist with heavy lifting?
- Do you have any ideas on how to make this process safer or easier?
The team brainstormed several potential solutions to address this safety concern. These included installing overhead cranes or lift assists, implementing a team lifting policy for heavy items, redesigning the workflow to minimize manual material handling, and providing ergonomics training and regular stretching breaks. After evaluating the options, they decided to install overhead cranes and provide ergonomics training.
The implementation plan involved installing overhead cranes in the cutting area, developing and delivering comprehensive ergonomics training, creating standard operating procedures for using the new equipment, and implementing a daily stretching routine at the start of each shift. The expected outcomes included a reduced risk of injuries, with reportable incidents decreasing, improved worker comfort and job satisfaction, increased efficiency in material handling, and a long-term reduction in workers' compensation claims and associated costs.
Tips for Success
To ensure your Gemba walks yield maximum benefits, keep these key principles in mind. Stay curious and open-minded throughout the process. Avoid making judgments or criticisms during the walk, as this can hinder open communication. Encourage employee participation and feedback to gain diverse perspectives on processes. Look for small, incremental improvements as well as big changes, as both can contribute significantly to overall efficiency. Always maintain a focus on analyzing and improving processes, not evaluating individual performance. By adhering to these guidelines, you create an atmosphere of trust and collaboration that enhances the effectiveness of your Gemba walks.
Also, check out our template to streamline your weekly Gemba walks.
Conclusion
Gemba walks are a powerful tool for prefabrication shop leaders seeking to drive continuous improvement. By consistently performing these walks and acting on the insights gained, you can unlock significant improvements in efficiency, quality, and employee engagement. Remember, the goal is not to catch people doing things wrong, but to understand the challenges in the processes and work together to find innovative solutions. With practice and dedication, Gemba walks can become a cornerstone of your shop's success strategy, leading to a more efficient, safer, and more productive prefabrication operation.